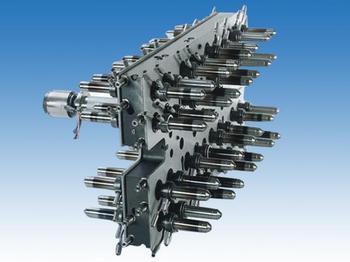
The hot runner is heated to ensure that the runners and gate plastic stay molten. Since the heating rod and the heating coil are arranged near the flow path or in the center, the entire flow path from the nozzle outlet of the injection molding machine to the gate is in a high temperature state, so that the plastic in the flow path is kept molten, and it is generally not necessary to open the flow path to remove the coagulation after shutdown. Material, only need to heat the flow path to the required temperature when you turn on the power.
The hot runner injection molding method was introduced in the 1950s. After a long period of promotion, its application penetration rate has increased year by year. In the mid-1980s, hot runner molds in the United States accounted for 15% to 17% of the total number of injection molds, Europe, 12% to 15%, and Japan, about 10%. However, in the 1990s, hot runner molds for plastic injection molds produced in the United States It accounts for more than 40%, accounting for more than 90% of injection molds for large products.
Advantages of Hot Runner Systems Saving raw materials and reducing product costs are the most significant features of hot runner molds. In a typical gating system, a large number of stalks are produced, and in the production of small products, the weight of the gating system may exceed the weight of the product. Since the plastic is always in a molten state in the hot runner mold, the product does not need to be trimmed, and basically no waste is processed, so a large amount of raw materials can be saved. Because there is no need for waste recycling, selection, crushing, dyeing and other processes, it saves time, saves time, and saves energy. Since the injected material is no longer incorporated into the recycled sprue material, the product quality can be significantly improved. At the same time, since the pouring system plastic remains molten and the pressure loss during the flow is small, the multi-gate and multi-cavity mold can be easily realized. And large-scale low-pressure injection molding products. The hot gate facilitates the pressure transmission, and can overcome the defects of plastic parts such as dents, shrinkage holes and deformation due to insufficient feeding.
Wide range of applicable resins, easy to set molding conditions. Due to the perfection and development of hot runner temperature control system technology, hot runners can be used not only in polyethylene and polypropylene with a wide melting temperature, but also in heat-sensitive plastics with a narrow processing temperature range, such as PVC. Polyoxymethylene and so on. Hot runner molding can also be achieved by using valve hot nozzles for polyamides (PA) that are susceptible to flow.
In addition, the simplification of operation and shortening of the molding cycle are also an important feature of hot runner molds. Compared with ordinary runners, the opening and closing strokes are shortened, which not only shortens the demoulding and molding cycles of the parts, but also facilitates automatic production. According to statistics, compared with ordinary runners, the molding cycle after using hot runners can generally be shortened by about 30%.
Hot Runner System Structure Hot runner system generally consists of hot nozzle, manifold, temperature control box and accessories. Hot nozzles are generally divided into two types: open hot nozzles and needle valve hot nozzles. Since the form of the hot nozzle directly determines the selection of the hot runner system and the design and manufacture of the mold, the hot runner system is often divided into an open hot runner system and a needle valve hot runner system.
Diverter plates are used in multi-cavity or multi-point feeds, single point feeds, but with feed port offsets. The material is usually P20 or H13. Dividing plates are generally divided into standard and non-standard two categories. The structure is mainly determined by the distribution of the cavity on the mold, nozzle arrangement and gate location.
Temperature control box includes host, cable, connector and wiring socket.
Hot runner accessories typically include: heaters and thermocouples, runner seals, connectors, and junction boxes.
Classification of Hot Runner Systems Generally speaking, hot runner systems are divided into single head hot runner systems, multiple hot runner systems, and valve gate hot runner systems.
The single head hot runner system consists of a single nozzle, a nozzle head, a nozzle connecting plate, a temperature control system, and the like. The single-head hot runner system plastic mold structure is relatively simple, the plastic in the molten state is injected into the nozzle connecting plate from the injection machine, and the cavity is injected after the nozzle reaches the nozzle head.
The multi-head hot runner system plastic mold structure is more complex. The molten plastic is injected into the nozzle connecting plate by the injection machine, flows through the hot runner plate to the nozzle, reaches the nozzle head, and then is injected into the cavity. Hot runner system nozzle and fixed template have radial size matching requirements and axial size limit requirements.
Valve gate hot runner system Plastic mold structure is the most complex. It has the same structure as an ordinary multi-port hot runner system plastic mold. In addition, a set of valve needle actuators control the opening and closing motion of the valve needle. The transmission device is equivalent to a hydraulic cylinder and is connected with the mold by the hydraulic device of the injection machine to form a hydraulic circuit to realize the opening and closing movement of the needle valve and control the injection of the molten state into the cavity.
H3 Led Headlight,H3 Headlight,H3 Headlight Led,H3 Led Headlight Bulb
CHANGZHOU CLD AUTO ELECTRICAL CO.,LTD , https://www.cld-led.com