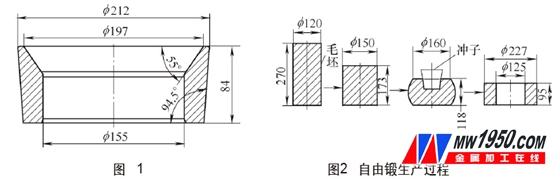
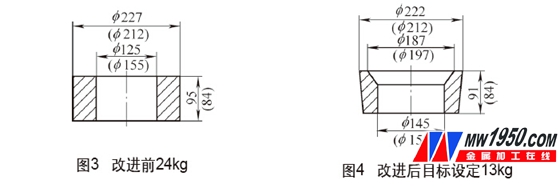
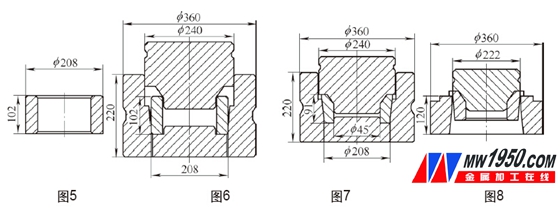
High Strength Steel Tie Rod are steel structural members made of carbon structural steel and alloy steel, processed by machining, heat treatment and surface anti-corrosion treatment, supplemented by adjusting sleeves, lock and joints etc. The Steel Tie Rod are important components of steel structures for construction of giant, large span buildings and ship docks. They are mainly used for prestressed parts and large span buildings in construction projects. While the strength of the product is improved, but the plasticity index is not reduced, which satisfies the principle of using the same amount of strength in the architectural design. The tie rods, tie bars, tension rods and tension bars steel grades are specified as grade 460, grade 520, grade 550, grade 650.
Architectural Tension Bar For Construction
Tension Bar,High Tensile Steel Rod,Structural Tension Rods,Architectural Tension Bar For Construction
SHANDONG LE REN SPECIAL STEEL CO., LTD. , https://www.chinasteelok.com