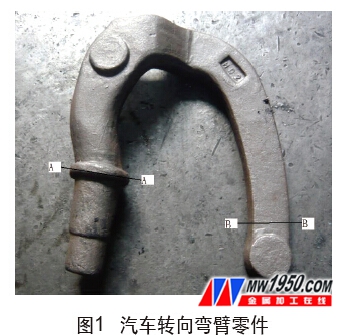

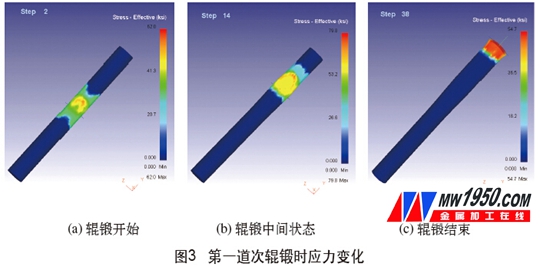
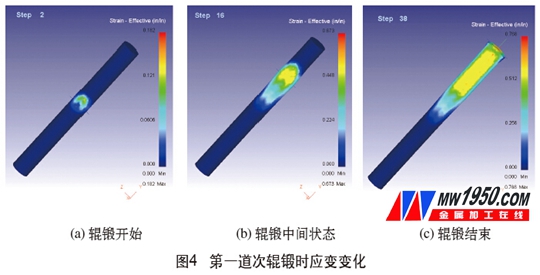
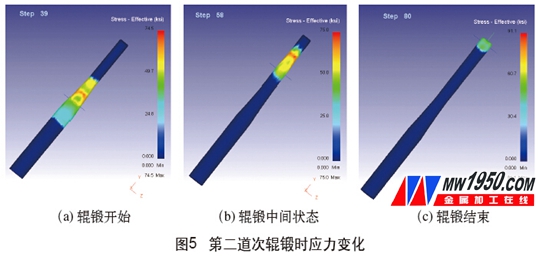
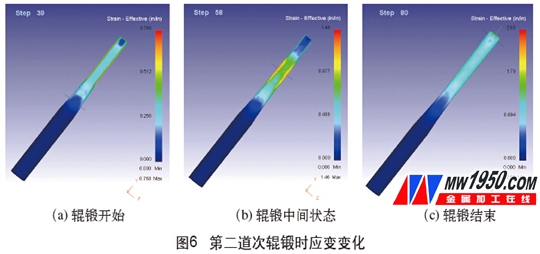
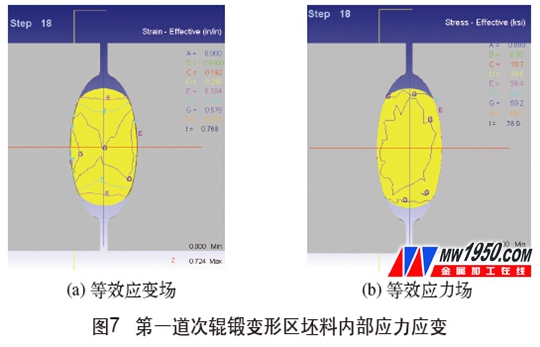
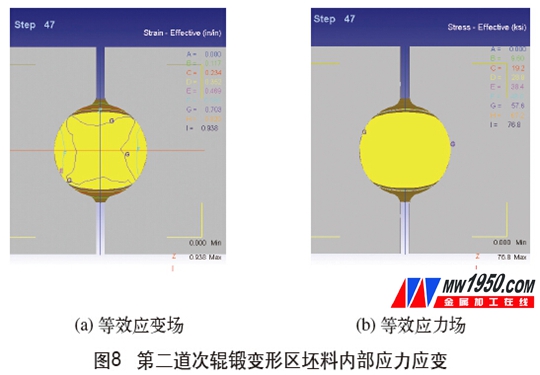
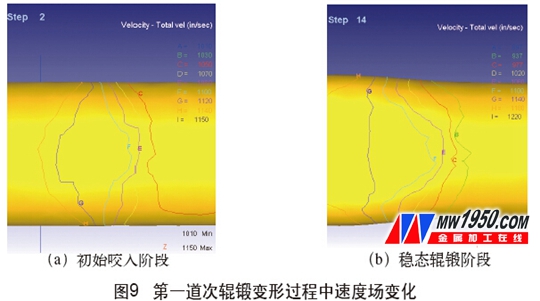
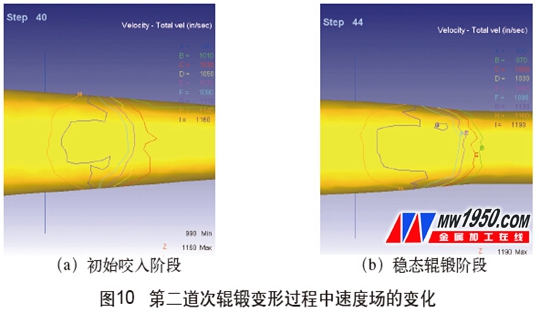
Single layer glass reactor is also called single wall glass reantor, non-jacket glass reactor. Comparing double layer jacket glas reactor, there is no jacket for heating or cooling circulation. The heating bath or heating mantle under the single layer glass reaction kettle is used for heating.
Stainless steel heating elements have been built into bath of single layer glass reactor for heating
You don't need more expensive heater circulator. You can do high temperature or nature temperature chemical mixing reaction for with this single layer glass reactor.
You can buy 1l 2l 3l 5l 10l 20l 30l 50l 100l 150l 200l single layer glass reactor from kori instrument factory. Exproof glass reactor is opyional for the glass reactor above 10l.
Support OEM & ODM and flexible custom service.
Chemical single layer glass reactor 1l 2l 3l 5l 10l 20l 30l 50l 100l 150l 200l with stainless steel water oi bath
Chemical single layer glass reactor 1l 2l 3l 5l 10l 20l 30l 50l with heating mantle for heating
Customized single layer glass reactor with collection or condenser into glass lid or others
Chemical Glass Reactors Including Single layer glass Reactors, Jacketed Double Wall Glass Reactors and Triple layer or Three Layer Glass Reactors .
Single layer Glass Reactors means the Big Glass Reaction Vessel just single layer or One layer and Always with Stainless Steel Water Oil Bath or Heating mantle for heating to make sure the chemical Reaction occurs
Single Layer Reactor,Glass Reactor Vessel,Single Layer Glass Reactor Price ,Single Layer Experimental Glass Vessel Kettle, Heating mantle Glass Reactors
Zhongyi Kori(Zhengzhou)Equipment Co.,Ltd , https://www.korireactor.com