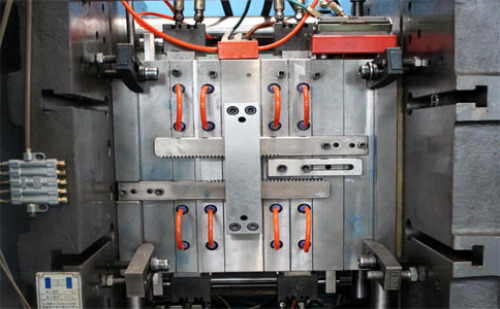
Introduction: Stacked molds are a new type of mold in which multiple pairs of single-layer molds are stacked and mounted on an injection molding machine for injection molding. The biggest difference between its technology and general injection mold technology lies in the fact that multiple cavities are arranged in a mold in the mold clamping direction. This technique greatly improves the injection efficiency.
Multilayer molds combine multiple subcavities in one pair of molds. The mold filling, holding pressure and cooling time are the same as single-layer molds, which greatly reduces the production cost of injection molding. The production efficiency is an ordinary single-layer mold. Multiplied or multiplied, greatly improving the production per unit time. In addition, single-layer mold injection molding machines can also use stacked molds, saving the cost of investing in additional machinery, equipment, and new labor. At the same time, when used with an injection molding machine, the laminating injection mold increases the clamping force by 5% to 10% compared with the conventional mold, and the output increases by 90% to 95%, which greatly reduces the cost and improves the equipment utilization rate. productivity.
Laminated injection molds are different from conventional mold design theory, so the development of a new set of mold design theory to guide the design of laminated injection molds becomes a top priority. The design points of the multi-layer injection mold will be described below. (1) When stack injection molds are used to check the maximum injection volume of the injection molding machine, it depends on the actual situation. Cold runners can be used, and hot runners can also be used. The use of hot runners allows for the production of non-returned aggregates, and the use of cold runners requires consideration of the amount of plastic used in the gating system. (2) Different plastic injection molding processes require different injection pressures. In the specific operation, the injection pressure of the plastic parts should be determined in combination with actual conditions and computer simulation flow analysis, and then compared with the injection pressure of the injection molding machine. (3) The stack extends the flow path, the pressure loss is greater than the conventional single-layer mold, so the injection pressure must also be increased accordingly, so to increase the clamping force, the safer way to check is to lock the same single-layer mold Mold force increased by 10% to 15%. (3) When the unsuitable central main nozzle causes the mold to close, the center main nozzle will not exceed the maximum distance the injection molding machine nozzle retreats or advances in the base. The current method is to ensure that the center main nozzle still remains in the fixed mold part after mold opening, so as to prevent the flash of the center main nozzle head from dripping onto the mold cavity wall.
The nylon mesh has white and black color, are widely used in all kinds of filtration and separation, such as:
1. air filter mesh in air conditioner filter
2. liquid filter mesh for milk, juice, cheese, soya bean ect.
3. flour, solid mesh for milling
4. We can deep produce it into filter bags, Filter Disc and filter strainers.
5. The microphone net
Smooth filament, immersion resistance, no material drop off.
Stable chemical and physical properties.
Nylon Wire Mesh,90 Micron Nylon Mesh,Wire Mesh Fabric Mesh,Nylon Filter Wire Mesh
Xinxiang Xin Ming De Machinery Co., Ltd. , https://www.xmdsieve.com