1 Main exhibits in the territory (1) JKM8320A CNC high speed concave camshaft grinding machine
This machine is an exhibit of Jiangxi Jieke Machine Tool Co., Ltd. It uses large and small grinding wheel to turn the combination and follow-up grinding to realize the roughing and finishing of the whole concave camshaft in one clamping, and can be equipped with automatic loading and unloading mechanism, suitable for the production line. .
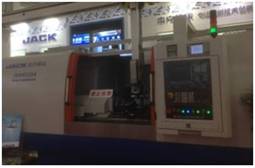
(2)MK8220/SD double wheel frame CNC cut point tracking crankshaft grinder
This machine is a national major science and technology special product, produced by Shanghai Machine Tool Works Co., Ltd., and has reached an order with Shanghai General Motors (SGM). The machine tool is a double-wheel CNC cutting point tracking crankshaft grinding machine, which can realize the external cylindrical grinding of the crankshaft main journal and the connecting rod neck in one clamping. It is suitable for the crankshaft grinding of the four-cylinder and six-cylinder machines of the engine production line of the automobile whole machine factory. . The machine tool adopts a horizontal layout and the wheel frame moves.
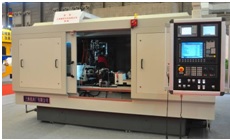
(3) B2-K1018 double wheel frame follower type CNC crankshaft grinder
Developed by Beijing No. 2 Machine Tool Works Co., Ltd., this machine is an ultra-high-speed precision grinding equipment for the precision grinding of the crankshaft connecting rod neck and spindle neck of automobile engine. It can realize the batching of crankshaft connecting rod neck and main journal with one clamping. Precision machining, suitable for use in crankshaft production lines. B2-K1018 is the scientific and technological achievement of the National 863 Program and the National Major Science and Technology Project, and won the 2014 China Machinery Industry Science and Technology Award.
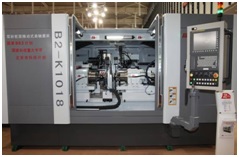
2 Major overseas exhibits
(1)JUCAM 6L camshaft grinding machine
According to the German JUNKER company, two sets of shafts with different diameters of grinding wheels are arranged on the front and rear of the machine wheel frame. The cycloidal tracking grinding process can be used to achieve camshaft grinding with various shapes such as concave and convex surfaces. The coarse and fine grinding can be completed, and the camshafts of various cylinder numbers can be processed through the replacement procedure to achieve high flexibility and high efficiency.

(2) LT2 (E) type crankshaft grinder (double wheel frame)
The Cinetic Landis Crankshaft Grinder in the UK is very special. The machine uses the follow-up grinding method to grind the crankshaft connecting rod neck or other journal. The machine has the center height, the whole machine volume, the grinding wheel size, the total power, the processing cycle, etc. The older generation of products has been optimized for better results.
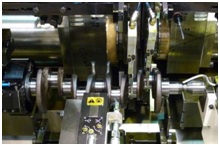
3 Conclusion
The crankshaft and camshaft are key components of the internal combustion engine. Throughout the various crankshaft and camshaft processing equipment of this exhibition, it can be seen that with the development of the automobile industry, the engine has also been upgraded and developed rapidly, and domestic and foreign related grinding products have also developed rapidly, and its main The trend is to increase productivity, increase automation and improve processing quality. For the products of this year's exhibition, the following three obvious characteristics are shown:
(1) In terms of application fields, concentrated in the internal combustion engine industry, especially in the passenger vehicle engine industry, medium and small crankshaft and camshaft grinding machines are developing rapidly, with a large number and fast update.
(2) As far as the technical level is concerned, the cutting point tracking grinding technology has become the mainstream, and the direct drive technology is widely used, and the proportion of the follower type crankshaft and camshaft grinding machine is increasing.
(3) In terms of equipment type, many famous crankshaft and camshaft grinding machine manufacturers no longer only focus on a single crankshaft and camshaft grinding machine, but on the entire crankshaft and camshaft machining production line, providing users with complete sets of equipment for the production line. And provide a complete technical solution for supporting services.
Of course, through the comparison of the domestic and foreign crankshaft grinding machines, we also clearly found that the development status of China's crankshaft grinding machines is not optimistic, there is still a certain gap in the reliability of domestic grinding machines, and the gap between software and control systems and human-computer interaction operability. Also more obvious. High precision, high efficiency and high reliability are still the direction that domestic crankshaft grinder manufacturers need to work hard.
Plastic Optic Fiber Patch Cord
The plastic optic fiber Patch Cord is low attenuation, no heat, flexible, widely use in different purpose. We have different purpose and different function pacth cord. All of the products has CE, ROHS, Reach certificate. Our workshop area more 10000sqm, and we have professional R&D.
The patch cable connects with two connector. This is for different purpose, to [patch" a signal from one side, switch, or router to another side, switch, or router. Use patch cables to carry a variety of signals, such as: ethenet, telephone, and other industrial area.
fiber optic equipment,fiber optic patch cord,fiber patch cord
Jiangxi Daishing POF Co.,Ltd , https://www.jxopticfibrelight.com